Concrete is a widely known building material due to its rock-solid robustness and versatility, but its durability confronts some wear and tear over time. Understanding its nature, types, and possible concerns and vulnerabilities is crucial. In this article, we will discover what concrete is, its different types, and common apprehensions, including cracking, staining, and erosion. We will help you learn the effective strategies for guarding concrete surfaces against these glitches, and the vital function of nano-ceramic coatings will also be highlighted. We will especially observe the immense benefits of the Nasiol Z Series that are accessible in water- and alcohol-based formulations. They are best known for keeping up surface breathability while increasing hydrophobicity. These highly recommended coatings are cured at room temperature. They aim to deliver long-term resilience by avoiding mold growth and minimizing structural wear and tear.
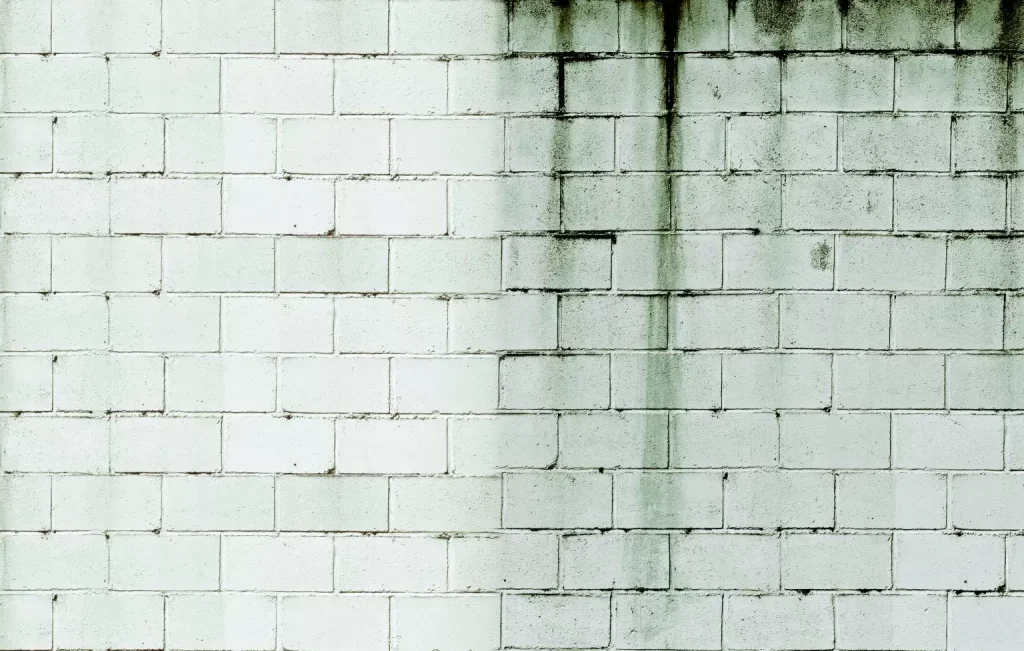
What are the Types of Concrete?
Understanding the various types of concrete is crucial for anyone working with this versatile building material. There are numerous types, including high-strength concrete, ready-mix concrete, stamped concrete, asphalt concrete, concrete aggregates, plain concrete, pumped concrete, precast concrete, and glass fiber reinforced concrete (GRC). Each type has its unique properties and uses, and a comprehensive understanding of these can greatly enhance your knowledge and skills in the construction industry.
Among the various types of concrete, precast concrete stands out as a popular and efficient choice. This type of concrete is formed into precise shapes at a factory and then transported to the construction site, making the process smoother and faster. It is widely used in construction materials, offering a level of efficiency and practicality that is distinct from conventional concrete. The use of molds to give concrete a desired look or shape further enhances its versatility and appeal.
Glass Fiber Reinforced Concrete (GRC): GRC stands for Glassfibre Reinforced Concrete or GFRC. GRC is a special type of concrete created by adding special additives to it. Steel is used as reinforcement in standard concrete. In GRC precast concrete structural elements, alkali-resistant glass fiber is used instead of steel. This protects the concrete from corrosive effects. In addition, the resistance of concrete against tensile and pressure is increased.
As well as being used for exterior building facades, GRC has also been used for many decades as an ornamental concrete. It has been used to create domes, statues, planters, and fountains; however, it is much more expensive than conventional concrete.
Ultra-High-Performance Concrete (UHPC): UHPC is exceptionally tough and heavy-duty. It is formed with fibers, fine powders, and a reduced water-to-cement ratio. UHPC is used in the construction of bridges, towers, and skyscrapers, as well as other structures that require extraordinary vigor and permanence.
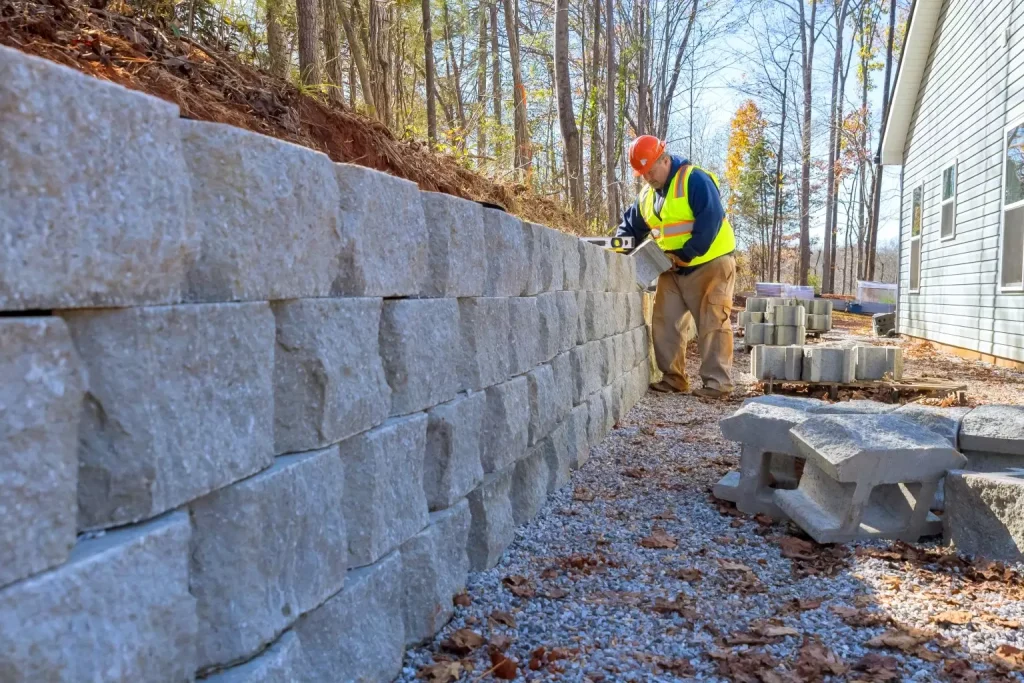
What Weakens the Concrete?
Many factors periodically make the concrete weak; let’s explore them one by one.
Water Penetration
When water penetrates concrete, it can oxidize the steel bars inside. This deterioration can lead to rust, which can further expand. This wear and tear can cause cracks and spalling. The persistence of water impairs the concrete matrix itself. It curtails, reducing its overall effectiveness and sturdiness over time.
Common Signs of Water-Damaged Concrete
- Cracking
There are several reasons why concrete can develop cracks. Cracks don’t always indicate a problem with water damage, but if your concrete has some cracks on its surface, it will be more vulnerable to additional water damage in the future. Because of this, it’s important to watch out for surface damage (such as extensive cracking), as this will let water into your already porous concrete, causing serious harm.
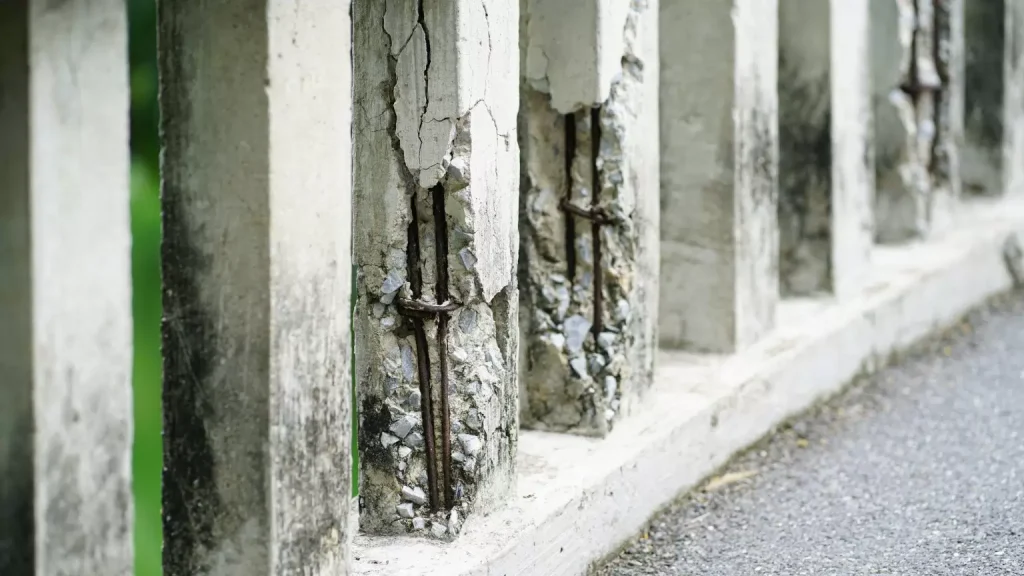
- Discoloration
Discoloration is another indication of water damage. One part of the concrete will be darker than the other due to the water present. Therefore, there’s a significant probability water is causing damage if you find sections of your concrete that are discolored and darkened.
- Scaling
Constant exposure to dripping water on concrete surfaces can lead to peeling or scaling, also known as spalling. The surface of the concrete peels off thin pieces. The cement layer gets brittle and soft when the entire surface is exposed to water dripping, which results in spalling. Water penetration can weaken the concrete structure and cause the surface to break apart.
- Efflorescence
One typical water-related problem that can harm concrete surfaces is efflorescence deposits, which appear on the concrete’s surface as powdery, white stains.
Water moves through the concrete and carries dissolved salts to the surface. Efflorescence deposits occur after the water evaporates, leaving salts behind.
- Mold or musty smell
Like most fungi, mold grows best in warm, humid conditions. Mold appears as black or dark green smudges and spots and usually occurs along the edges of flooring, sometimes crawling up walls. Although it could initially seem like dirt, mold is far more challenging to get rid of. Therefore, if mold has started to form on your concrete, it’s safe to infer that water has gotten into the material.
- Hydrostatic pressure
Hydrostatic pressure is created on a home’s foundation by any source of running water, such as rain or plumbing line leaks. The foundation walls will crack or bend because of that pressure. One of the causes of this pressure is expansive soils like clay. When these soils are wet, they expand against the foundation; when they get dry, they shrink back again. Over time, this cycle causes significant damage to the concrete foundation by causing it to shift back and forth. Furthermore, water never accumulates uniformly, therefore pressure is nearly always distributed randomly. Horizontal cracks in the concrete foundation of the house occur from the stress placed on different areas of the structure relative to one another.
Decomposition Of Reinforcing Steel (Rebar)
Concrete uses steel reinforcement that offers tensile strength. When this steel rusts due to extreme contact with wetness, oxygen, and chlorides, it grows further and can lead to internal pressure, further leading to cracking and weakening of the surrounding concrete.
Poor Mixture Formulation
The potency and toughness of concrete dramatically depend on its mix proportions. Inaccurate ratios of water, cement, aggregates, and enhancers could result in a concrete mix that is too puny. This mix is prone to cracking, resulting in contraction and expansion under diverse conditions.
Harsh Temperatures (Freezing and Thawing)
Concrete expands when heated and shrinks when cooled. In areas with fluctuating temperatures, repetitive spells of freezing and thawing can put pressure on the concrete, leading to cracks and surface breakdown. One reason that shortens the concrete’s life in cold climate zones is the freezing of water seeping into the concrete.
Chemical Decomposition
Concrete can be susceptible to chemical deterioration from compounds, including chlorides, acids, and sulfates. These intense chemicals can respond to the cement matrix or the reinforcing steel, resulting in erosion and decline of the concrete with time.
Erosion
Another cause of concrete weakness is erosion. Physical processes like water flow and abrasion gradually affect the outer surface of concrete, exposing the underlying layers to further damage. This continuous surface degradation weakens the concrete’s structure and strength.
Cost of Concrete Maintenance and Repair
There are various factors that contribute to the maintenance and repair of concrete, such as labor costs, material costs, equipment costs, downtime costs, and frequent repairs. You need to have skilled labor to inspect the repairs, after which material will be required to fix the issue while using the specialized equipment. Frequent repairs, without adequate protection, concrete structures may require frequent repairs due to wear, weathering, and chemical exposure.
Nanocoatings can effectively reduce the cost of these factors with their enhanced durability, water repellency, chemical and UV resistance, and longer lifespan. Nasiol Z Series Nanocoatings help to improve the performance of concrete.
What Makes the Concrete Surface Durable?
The endurance of concrete is inevitable and plays a pivotal role in ensuring structures sustain intense weather conditions and other external factors over time. Concrete is resilient because of its chemical formulation and physical composition, strengthening it against several forces. Despite its toughness and durability, concrete may deteriorate and undergo discoloration, crack, and rust. Temperature shifts and exposure to water and harsh chemicals significantly threaten concrete’s durability. The question is whether the concrete can be protected from deterioration or not. And the answer is YES; if proper and precise measures are taken, concrete surfaces can be more resilient and durable. Nano coatings and a few procedures protect concrete surfaces from these factors.
Nanocoatings offer immense perks for the protection of concrete surfaces; let’s discover:
Nanocoatings, like those in the Nasiol Z series, play a significant role in enhancing concrete durability. These coatings create a protective barrier that prevents water and contaminants from penetrating the concrete surface. They achieve this by forming a hydrophobic barrier, which repels water and reduces the risk of water-related issues like mold growth and cracking.
Water and oil repellency effect: The Nasiol Z series of nanocoatings produces a hydrophobic shield, repelling water from entering concrete surfaces. They also repel dirt and oil contaminants, so the coated surfaces stay clean for a longer time.
Mold prevention: Nasiol Z series of nanocoatings prevent mold growth; they remarkably preserve the integrity and visual appeal of concrete surfaces. They prevent water penetration into the concrete so that surfaces are protected from issues including mold growth, staining, and degradation of surface finishes. You can learn more about mold prevention from our previous blog.
Breathable coating for concrete: The Nasiol Z series of nanocoatings is breathable. They do not close the pores of concrete surfaces and allow them to breathe.
Chemical and UV resistance: The Nasiol Z series maintains the appearance of the concrete surfaces with its chemical and UV resistance properties. It prevents discoloration on concrete which occurs over time due to exposure to UV light, chemicals, or organic matter such as leaves or stains.
Fast and easy application: The Nasiol Z Series is applied by manually spraying onto the surface, or pressurized spraying is possible for industrial applications. Our nano coatings are curable at room temperature and accelerated curing is possible by applying heat.
Endurance: The Nasiol Z series improves and enhances resilience and prolongs the lifetime of concrete structures. It is a durable choice for concrete protection. Even on high-traffic horizontal surfaces, the alcohol-based product Nasiol Z has a durability of up to 2 years, and the water-based product Nasiol Z-WB has a durability of up to 3 years.
Low Maintenance Cost: Nano-coated concrete is well protected, so it dismisses the urge for frequent cleaning and expensive maintenance. Nasiol Z Series of nanocoatings create easy-to-clean surfaces. Additionally, they will save on labor costs by reducing the time spent on maintenance and repair.
Environmentally Friendly: The Nasiol Z series of nanocoatings is environmentally friendly. They offer sustainable fortification for concrete surfaces. They are REACH and low-VOC certified products, friendly to the environment and human health.
Conclusion:
In conclusion, Nasiol Z series nano coatings are highly effective solutions for concrete glitches like mold growth, cracking, staining, and erosion. By creating a protective shield that maintains breathability and hydrophobicity, these coatings ensure that concrete surfaces remain intact and visually appealing over time, even under harsh environmental conditions. This makes them a preferred choice for enhancing concrete durability and longevity in various applications.
Nanocoatings can effectively reduce the cost of these factors with their enhanced durability,
water repellency, chemical and UV resistance, and longer lifespan.
FAQs
What is the benefit of nano coating on concrete surfaces?
Nanocoatings promise to deliver numerous perks for shielding concrete surfaces. They aim to offer a defensive barrier that guards concrete from discoloration, staining, cracking, and water diffusion. These coatings generate a nanoscale fence that efficiently obstructs damaging substances from approaching and ruining the concrete surface.
How do you protect concrete from water?
Water-repelling nano coatings are the best remedy for protecting concrete surfaces from water. Nanocoatings work as waterproofing coverings that avert water from entering the concrete. It dismisses the possibility of decay from water.
How to stop concrete from water damage?
Nanocoatings offer advanced solutions to prevent water damage in concrete structures due to their ability to form highly effective barriers against water penetration. The Nasiol Z Series of nano coatings exhibit hydrophobic properties. This reduces the ability of water to adhere to the concrete surface and penetrate the material. The Nasiol Z Series is designed to be breathable, allowing water vapor to escape from within the concrete while preventing liquid water from entering. This feature is crucial for maintaining the internal water balance of the concrete.
How do you prevent mold growth in concrete?
Averting mold growth in concrete involves ensuring suitable drainage systems, sufficient aeration, and utilizing anti-mold nano coatings. These precise measures help keep dampness levels low and generate a healthy environment that keeps mold growth at bay.
How to make concrete waterproof?
Waterproofing concrete relies on using practical techniques, including applying waterproof nano coatings. Waterproofing membranes are typically applied to create a barrier against water penetration, while nano coatings utilize nanotechnology to form a protective barrier at the microscopic level.